
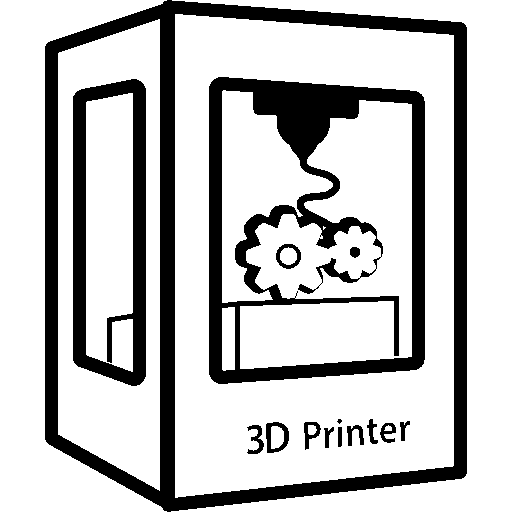
Images don’t directly load for me so I only saw a few (copy pasted to browser).
It’s going to depend on what you want to do with it and at what point you’re happy. I did the following with mine and then heavily borrowed from it for my Ender 5 Pro that’s enclosed printing Polycarbonate Nylon and ASA for automotive parts:
-
Ferrules for all screw terminals that are using wire currently. It is dangerous to not have these and they are super easy to install, plenty of videos on how to do it I bought a kit with the crimp tool for like $15 and your house won’t burn down lol. Make sure the connection between the wire and crimped ferrule is tight, if it’s loose at all remove it and do a new one.
-
Skr e3 v1.2 main board (this came with it when I bought it, buy something else you can’t do some more modern stuff like G34 with this I don’t believe, my Ender 5 Pro is just stock here).
-
bltouch, crtouch, the printed one that reuses the Z endstop, whatever one you will want some sort of bed probe to both reliably home the printer and allow you to auto level the bed.
-
Silicone bed spacers. Stock springs are crap, level silicone bed spacers once and you’ll never touch those knobs again (make sure there’s a little tension on the knobs when you’re levelling them initially though or they will back off!)
-
double sided PEI sheet with high temp magnet. The hictop you have is exactly what I have on both. Much more reliable adhesion I clean it with dawn dish soap and a wet paper towel then rinse and dry with a dry paper towel and I don’t need a glue stick for ASA. Allows for higher temps on the bed as well (how I preheat the Ender 5 Pros chamber typically, though the flat side is starting to delaminate a little after a year). Glass is ok but if you’re impatient at all you’ll rip a chunk out of it. Also never use that damn scraper everyone I know who has including myself has a scar from it lol
-
rPi3 with Klipper firmware (biggest upgrade, takes effort, might be able to do sonic pad easier but I’ve never used one). Sending prints straight to the printer and having a web UI is extremely worth it. Add a cheap webcam and you can hook into a selfhosted Obico for AI failure detection. I used an adxl345 for resonance compensation and it helped a ton along with pressure advance (using Ellis’ pressure advance tool not the Klipper cube print you measure) and the print quality is amazing at speed compared to the garbage that used to come off of my printer.
-
Buck converter in a frame mounted case off of main PSU, steps to micro USB connector to power the Pi off of the PSU, more of a nice to have so everything powers on together, try to remember to power Klipper down in the web UI before shutting the red switch off though so you aren’t killing power to it when shutting down.
-
90mm noctua fan and shroud for the Power Supply since that tiny fan was loud as hell even with the shroud
-
Speeddrive printed direct drive with a pancake stepper so the motor clears the frame (I’ve done this on two printers, there is no reason to buy an expensive direct drive setup). I got a BMG clone with this and it has been decent, the grub screw came loose once so I used blue thread locker on it and it’s been fine for a few years. It’s extremely well balanced weight wise compared to some of the super front heavy ones you’ll find on Amazon etc.
-
Either get a filament dryer and print a filament guide that’s raised enough for the Speeddrive to clear it when at full height. Or rotate the filament spool 90 degrees with a new mount that’s raised enough for when the printer height is maxed to retain the full height.
-
If not using a filament dryer, Print a spool holder that uses bearings you purchase so it moves more freely than the stock one where the spool is just dragging.
-
Bimetal heatbrake from Slice engineering. Helps avoid jams, allow printing higher temp filaments. You do NOT need an all metal hotend with this, use the stock red one it’s all you need. My Ender 5 came with a Microswiss all metal hotend that is significantly less easy to work with using the same materials and jams occasionally. I used their boron nitride paste as well but no idea if it’s actually better than others the tube has lasted me a while.
-
Upgraded nozzle if you need, I did stainless steel for one printer and hardened steel on another that prints abrasives and carbon fibers, stainless needs a bit more heat (~260-270C for PETG on stainless at 100mm/s 3.5k accel)
-
Gulf coast robotics heater block temperature sensor. Glass bead one isn’t supposed to be used over a certain temp so upgraded this at the same time as the heatbrake for 300 degree C filaments
-
Noctua 4020 fan for hotend and dual 5015 blower fans with the Satsana duct that has removable vents. This made the printer nearly silent when done with the power supply fan. I print PETG around 20-30% fanspeed for the blowers and have never had it jam with the bimetal heatbrake but I have never ran this stock.
-
Cable chains to clean up the appearance mostly and prevent snags.
-
Dual Z motors. If you have a good main board that can level this (G34 I think?) this will make your printer way more reliable. If you don’t, print X axis gantry tramming blocks where you raise Z to around 50mm tall then place blocks under each side of the beam, shut steppers off then slowly twist the stepper motors on each side the same direction to lower the gantry onto the blocks, one side will usually reach a block well before the other. Once lowered, hit home and then quickly remove both blocks and allow it to home, your gantry should now be square and ready to level the printbed. This is a good time to check the wheels for the X axis and make sure they all feel right and not too loose/tight as they were likely adjusted with this skewed initially.
Hopefully that’s it, it’s a lot of stuff, for me most of it was spare parts or relatively inexpensive and done over a period of time which was much more doable than buying a more expensive or even new printer upfront. The upside is I know how it works inside out and any issues I can figure out within a minute or two usually. You don’t need to go this way but it worked extremely well for me so just wanted to throw it out there so you could pull ideas from it.
I would research these each separately, ones where you start relocating things you may need to extend or replace a harness with a longer one. Apart from that this took me about a year of just researching and trying things to figure out but it’s been an extremely reliable setup and a lot of it is printed which is a bonus. I can probably find links to stuff if you need as well I saved most of it I believe.
Hammering the model off is how I lost a quarter inch of glass out of my bed haha thats when I switched to PEI and just flex the plate to remove stuff now. PETG and glass never really got along for me though and I primarily print that on my 3.
Correct it turns it all metal, I just remember being back and forth on what else I needed to buy at that point and really just a good heatbrake does wonders, no larger heat sink or anything at least not until you start changing other stuff up.